Från kapacitetsbrist till ökade konkurrensfördelar
”Tack vare produktionsuppföljningssystemet e-PI har vi upptäckt oönskade flaskhalsar i vår produktion som motsvarar en besparing på över 1 miljon kronor per år.
Numera ligger maskinutnyttjandet på mellan 70–80%, vilket motsvarar en förbättring på drygt 40 %.
Tack vare fakta och information från systemet har vi kunnat vidta åtgärder som inneburit möjligheten att investera i andra maskiner och förbättringar samtidigt som man får behålla kunder i ett mer konkurrensutsatt läge från Östeuropa.”
Daniel Jansson, Produktionsledare på Forserum Safety Glass
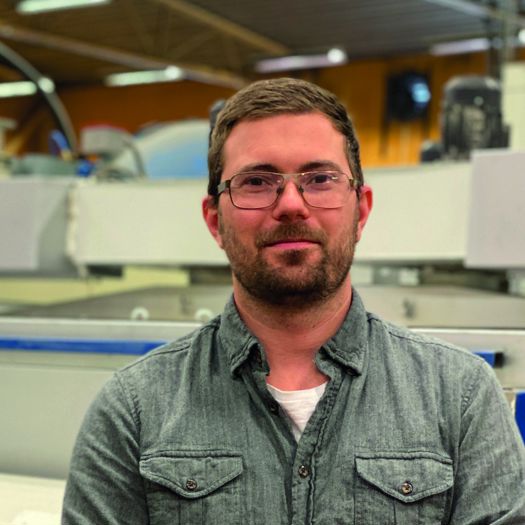
Problemet
Forserum Safety Glass AB (FSG) är ett av Sveriges ledande planglasföretag. De utvecklar och producerar produkter av förädlat planglas åt tillverkningsindustrin samt byggnads- och anläggningsindustrin i Norden, med fokus på Sverige.
Med hjälp av den information som fanns tillgänglig i affärssystemet hade företaget kontroll på kostnader som var kopplade till producerat glas som var nödvändigt för att kunna prissätta deras produkter utifrån följande parametrar;
- Antal producerat glas per skift
- Antal kvadratmeter
- Antal personer per skift som då delat på ovan parametrar
Det som saknades var mätningar på hur ofta maskiner stod stilla och varför. Det hade inte gjorts några mätningar på detta område tidigare.
För att kunna möta den ökade konkurrenskraften beslutade företaget att man behövde hitta ett intelligent mätsystem för att samla in vad olika typer av flaskhalsar berodde på i detalj. En av de maskiner som användes vid lamineringsavdelningen innebar en stor flaskhals.
Trots att maskinen kördes 2-skift var den ständigt fullbelagd och de 7 operatörerna som jobbade vid maskinen hade svårt att hinna med företagets kundleveranser.
Denna kapacitetsbrist ledde till att företaget fick tacka nej till större jobb och därmed tappade intäkter.
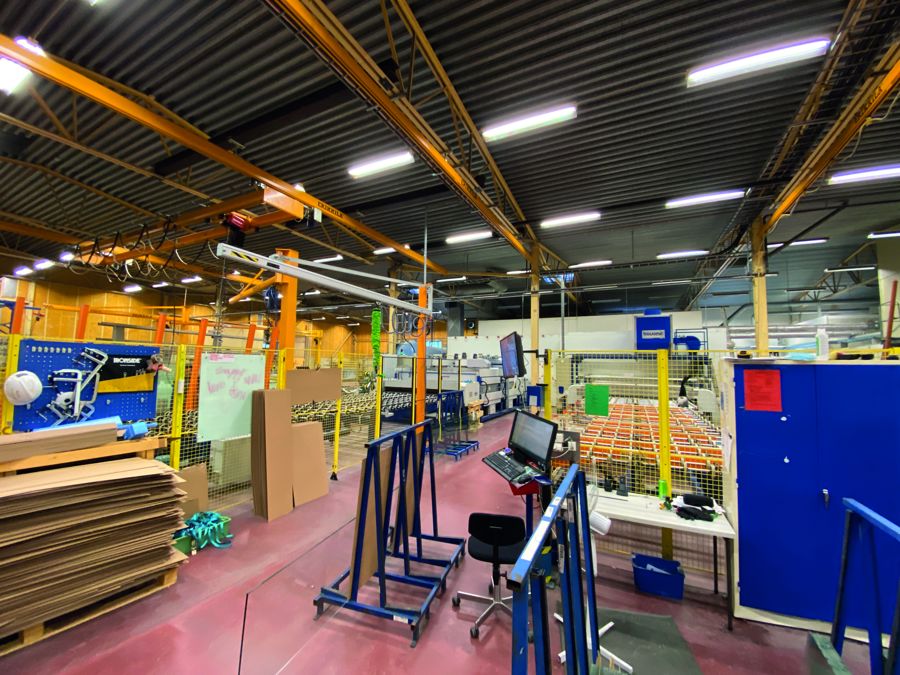
Lösning
Flertalet ledande personer i företaget hade arbetat med både Lean-utbildning av förmän och andra förbättringsåtgärder men lyckades ändå inte effektivisera befintlig maskinlinje utan att utöka med fler operatörer eller fler skift.
Ledningen insåg att något var tvunget att göras och bestämde sig då för att ta kontakt med oss på INVID och i samband med detta informerade vi om vårt produktionsuppföljningssystem e-PI.
Med hjälp av INVIDs verksamhets- och systemkompetenser insåg FSG möjligheten och potentialen med att undersöka om det fanns tid i maskinen som inte var utnyttjad.
Alla blev omgående inblandade av införandet av det aktuella systemet. Ledningen var tydlig med att personalen själva skulle spela en stor nyckelroll i projektet. Ingen trodde i detta skede på att systemet skulle kunna göra skillnad, då alla medarbetare verkligen kämpade för att hinna med.
Efter endast några dagars mätningar upptäckte man att maskinen endast hade en utnyttjandegrad på 30 procent.
Företaget ställde sig då frågor som:
- 30 % låter lite för orealistiskt för att vara sant
- Vad har vår personal gjort sedan maskinen införskaffades?
Det första FSG gjorde var att ringa till INVID och fråga om det var något fel på systemet eller mätmodulen, för sifforna kunde väl knappast stämma, de tyckte att detta var helt omöjligt.
Efter jämförelser med deras affärssystem visade sig det dock snabbt att de siffror som presenterades stämde till punkt och pricka.
Efter några veckors mätningar och manuella kodningar från operatörernas sida fick man bland annat information via rapporter som belyste grundproblemet; logistiken kring maskinen.
Det innefattade störningar som exempelvis byten av glastyper, letande efter material, vagnbyten och framtagning av specialfolier.
FSG började direkt med att först identifiera de olika problemområden och därefter började de sätta upp olika åtgärdsplaner.
Efter dessa åtgärder började företaget producera lika många detaljer på 8 timmar än de tidigare gjort på 16 timmar med samma produktionskapacitet. Eftermiddags-skiftet fick istället vara en del av förmiddagsskiftet och agera som materialförsörjare så att maskinen alltid är redo för nästkommande körning.
Idag har lamineringsmaskinen inga problem som är kopplade till logistiken kring maskinen.
Effekten
Med hjälp av produktionsuppföljningssystemet hittade man oönskade flaskhalsar i sin produktion och lyckats ta bort ett helt skift vilket motsvarar en besparing på över 1 miljon kronor per år.
I den aktuella flaskhalsmaskinen kan man numera producera lika många detaljer på 8 timmar som de tidigare hade gjort på 16 timmar med samma produktionskapacitet. Idag ligger maskinutnyttjandet mellan 70–80%, vilket motsvarar en förbättring på drygt 40 %.
Kunden upplever att det fortfarande finns förbättringar och potentialer att arbeta med. Med hjälp av fakta och information från lösningen har FSG ändrat sitt arbetssätt till att vara mer organiserat och strukturerat med en tydligare arbetsfördelning.
Ingen av operatörerna behöver slita så hårt idag som man tidigare gjort. Förmännen och produktionsplanerare får idag en snabb överblick från systemet vilket har inneburit till ett tydligare och bättre planeringsansvar. Ledningen och styrelsen får automatiska rapporter direkt från systemet.
Tack vare fakta och information från systemet har företaget kunnat vidta åtgärder som inneburit möjligheten att investera i andra maskiner och förbättringar samtidigt som man får behålla kunder i ett mer konkurrensutsatt läge från Östeuropa.
Tack vare lösningen har man utökat till flera maskiner och fortsätter att jobba med ständiga förbättringar.
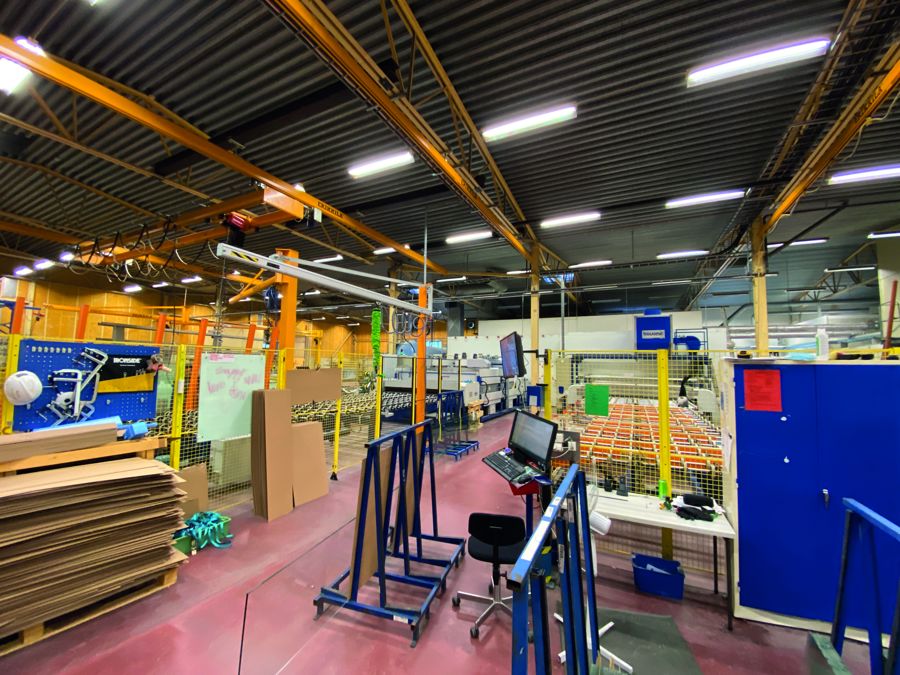
Kort om Forserum Safety Glass
Forserum Safety Glass AB (FSG) är ett av Sveriges ledande planglasföretag. De utvecklar och producerar produkter av förädlat planglas åt tillverkningsindustrin samt byggnads- och anläggningsindustrin i Norden, med fokus på Sverige.
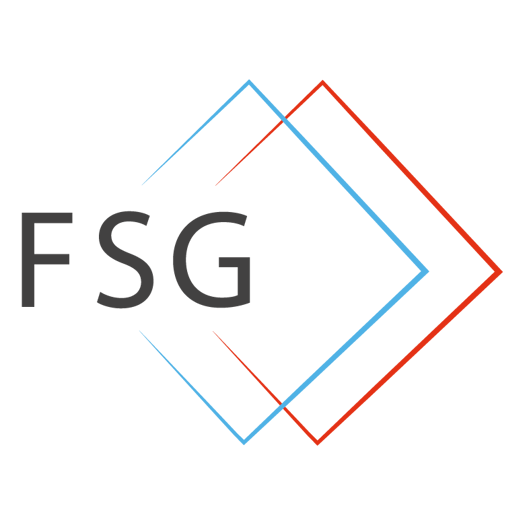
Önskar du fler referenser inom Smart Industri 365?
Samtliga tjänster inom Smart Industri 365
ePI Produktions-uppföljningssystem
Verksamhetsoptimering/ Konsulting - Smart Industri 365
PoV (Proof of Value)
Onlineutbildning
Kontakta oss om du önskar flera referenser från vår sida inom Smarta processer!

Fler referenser
AJ Produkter - Effektiviserad klienthantering och höjd IT-säkerhet
Hillerstorps Schakt - Smart lösning för service, underhåll och internkommunikation
Vill du veta mer om vad vi gör och vad som är på gång?
Skriv upp dig här, så får du ta del av nyheter, tips och trix och inbjudningar.